I had the pleasure of working with Ed Carpenter on the Harvest Sculpture installed in Lincoln, Nebraska in August of 2016.
Fabrication
Welding pipe
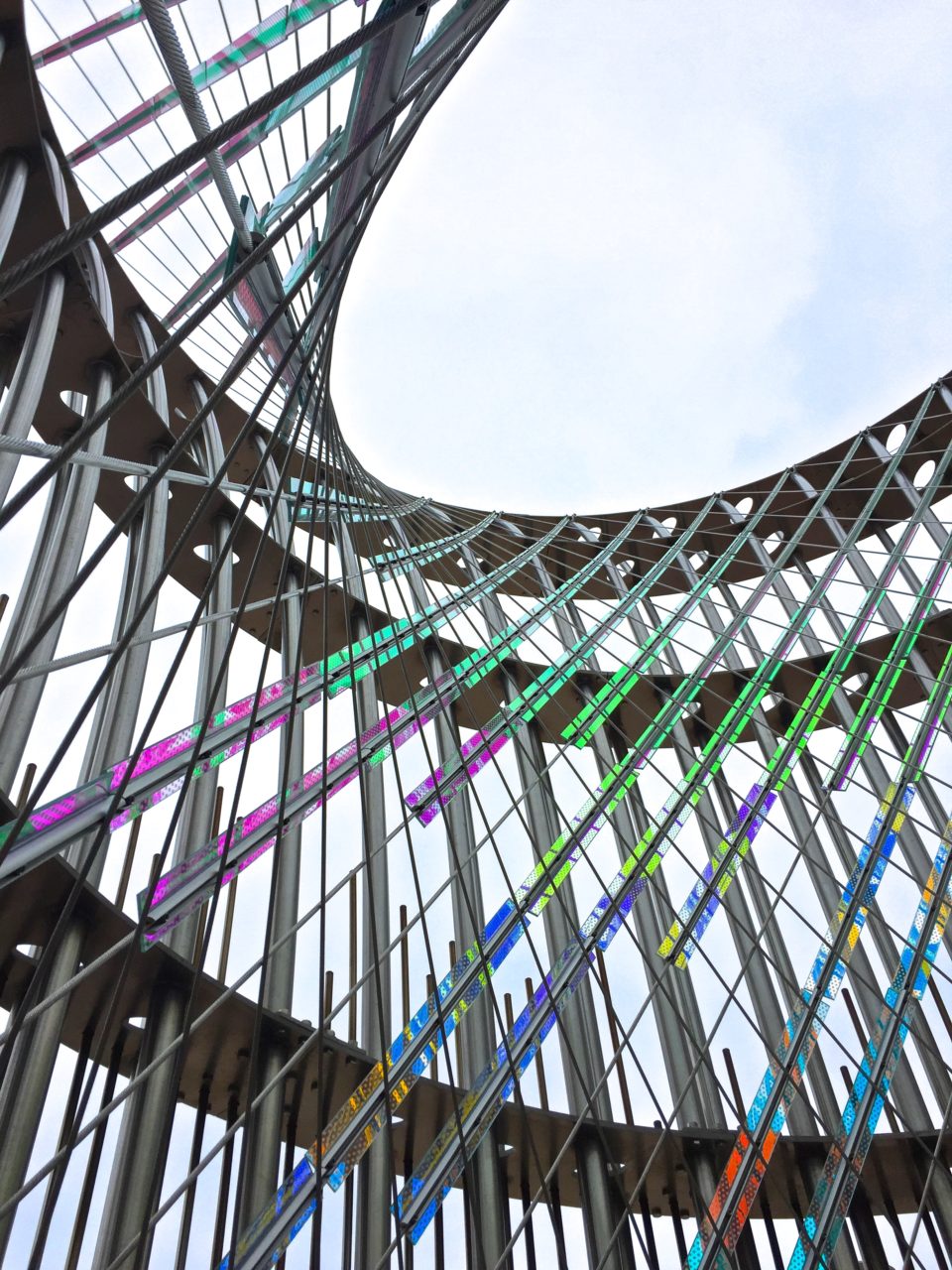
The pipe arrived in lengths about half what they needed to be, so we used an orbital TIG welding machine to join two sections of pipe into their final length.
Since the pipe were stainless steel, we used a contraption to back-purge the inside of the pipe with Argon gas to protect the root side of the weld. When welding stainless steel, excessive temperatures with exposure to oxygen causes oxide burn-through, or sugaring, which is basically the nickel and chromium burning out of the base metal.
The trouble is, the nickel and chromium are what make the stainless, well, stainless. Argon back-purging the interior of the pipe removes the oxygen environment and prevents this sugaring from concurring.
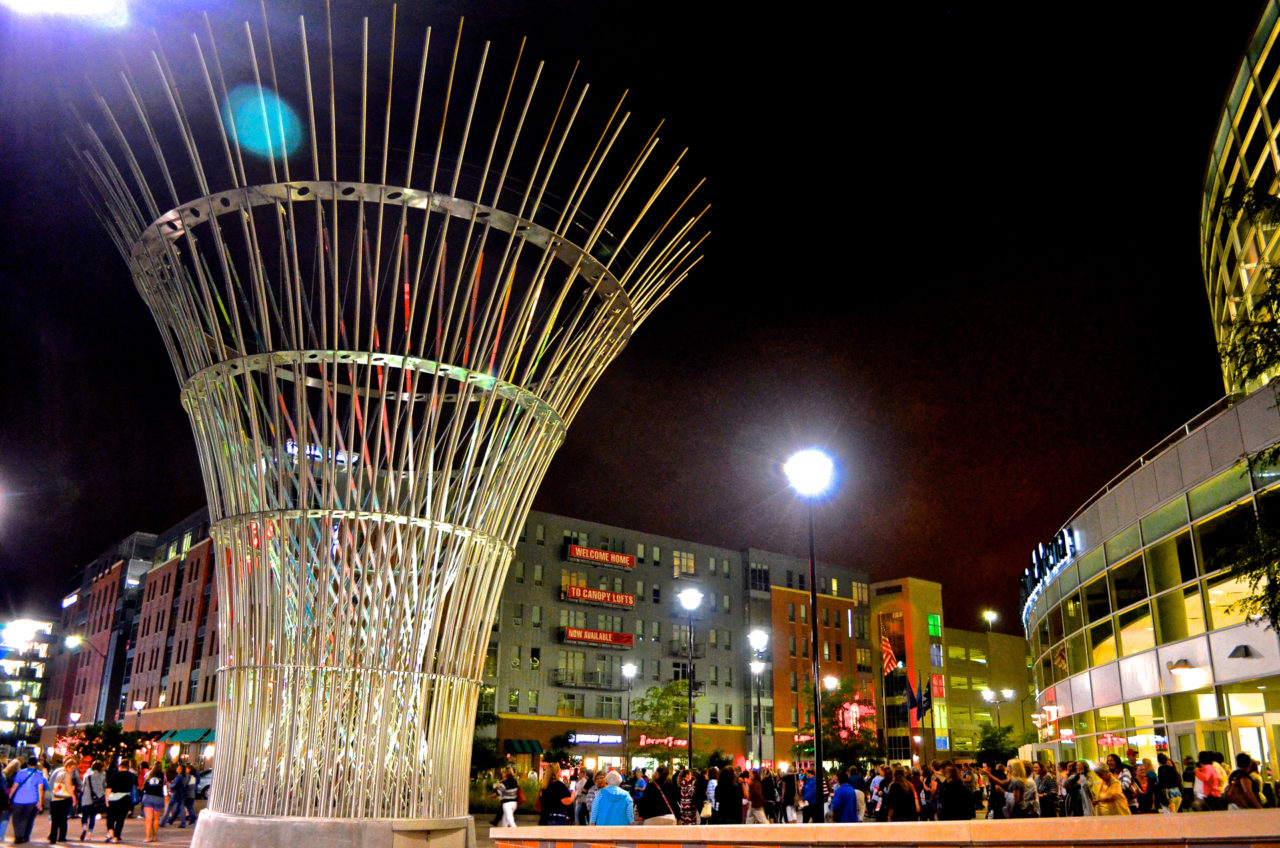
The last step is to test the welds using ultrasonic inspection, a form of non-destructive testing (NDT) to ensure there were no cracks or voids or porosity in the welds.
Polishing
After welding the pipe together, the excess weld reinforcement (the visible hump that looks like the weld) is ground flush with the pipe and the area is polished to match the surface finish of the pipe.
Roll Forming
The pipe was then rolled to have a gradual curve, resembling a stock of wheat pinched at it’s center. A hydraulic three-point slip-roll was used with custom made dies.
Burnishing the Ends
The ends of each pipe were to be discolored, similar to the change in features of the top of a wheat stock. Discoloring the pipe in a predictable and repeatable way was made possible by using inductive heating. We used a thick-walled pipe as an oven, and heated it with a purpose-built inductive heating apparatus. The thick-walled pipe would get red hot, then we would slide a stainless pipe into the end of the hot oven to burnish their ends.
Installation
The base plates, with anchors which would be embedded in concrete, were custom matched to the lower plate of the sculpture.
I attended the placement of these anchors to assist and approve of the placement and orientation of the anchor plates. The experience was great, seeing the beginning of the on-site work prior to the sculpture being installed months later.